Two reports highlight digitalization challenges in the chemical industry
In the past five years, the chemical industry has witnessed remarkable strides in digitalization, but the road to transformation remains fraught with challenges. Two pivotal reports, the 2018 "Innovation Plan i4.0: Route Towards a Digitized Chemical and Plastics Sector in Flanders" by Catalisti and its partners, and the 2023 "Digital Technologies for Sustainability in the European Chemical Industry" by CEFIC, offer a compelling narrative of how far the industry has come and what hurdles still lie ahead.
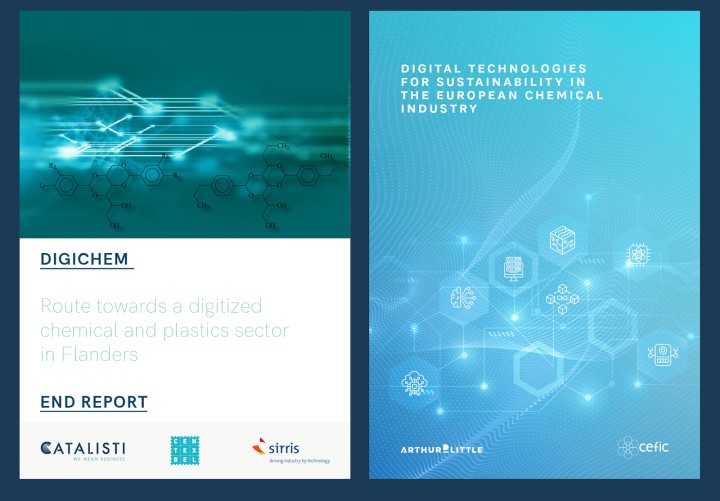
In 2018, the DIGICHEM project painted a picture of cautious optimism. Industry 4.0 was hailed as a revolution that could turn chemical plants into "smart factories" powered by automation, big data, and interconnected systems. Yet, many companies in Flanders approached these technologies with a "wait-and-see" attitude. Despite its reputation for innovation, the region's chemical sector faced significant barriers, ranging from the sheer complexity of retrofitting legacy systems to a lack of skilled personnel capable of navigating the intricate web of digital tools.
Fast-forward to 2023, and the digital landscape looks markedly different. Sustainability has taken center stage, as underscored in CEFIC’s report. Digitalization is no longer seen merely as a pathway to operational excellence but as a cornerstone of the European Green Deal. Artificial intelligence, blockchain, and digital twins are no longer aspirational buzzwords; they are practical tools helping companies reduce greenhouse gas emissions, optimize resource use, and design circular supply chains. But the CEFIC-report also notes:
The chemical industry’s sustainability journey is often referred to as the ‘quadruple challenge’ or the ‘double twin transition’: a circular and climate-neutral economy, Safe and Sustainable-by-Design chemicals, and concurrent digital transition. Given the closely connected nature of these objectives, it is surprising to see a lack of clarity around many of the key components required to achieve them, such as in how the transitions interrelate on a practical level, which technologies to apply, collaboration across the ecosystem, regulatory frameworks, and roadmaps of where to start.
To harness the potential of data
Hence, the challenges persist. One recurring theme from both reports is the struggle to harness the full potential of data. In 2018, companies were overwhelmed by the sheer volume of information being generated. Many lacked the infrastructure to process and analyze this data effectively. By 2023, the industry had made strides in deploying advanced analytics, but the gap between data collection and actionable insights remains a pressing issue. As one chemical executive put it, "We have more sensors than we know what to do with. It’s like being handed a library of books in a language you can’t read."
"We have more sensors than we know what to do with. It’s like being handed a library of books in a language you can’t read."
Cultural resistance to change also continues to hamper progress. In 2018, DIGICHEM highlighted a lack of digital literacy and leadership buy-in as critical obstacles. Five years later, while the industry’s mindset has evolved, many companies still struggle to fully integrate digital practices into their organizational DNA. Anecdotes abound of operators using augmented reality tools for maintenance tasks only to revert to manual methods out of habit or mistrust in the technology.

Collaboration across value chains
The rise of sustainability as a driving force has added new layers of complexity. Where the 2018 report focused on internal efficiencies, the 2023 report underscores the need for collaboration across value chains. Companies are being called upon to share data securely and transparently with suppliers, customers, and even competitors. Blockchain has emerged as a potential solution for traceability, but trust and standardization remain significant barriers. One logistics manager recounted the irony of using cutting-edge technology to trace recycled materials, only to face delays because upstream partners were still using paper records.
Why use Augmented Reality?Augmented reality (AR) has emerged as a transformative tool for the chemical industry, offering solutions to some of its most pressing challenges. By overlaying digital information onto physical environments, AR allows operators to visualize complex data in real-time, whether it's through smart glasses or mobile devices. Maintenance tasks, for example, can be performed more efficiently with AR-guided instructions, reducing downtime and minimizing errors. A notable success story comes from a leading European chemical plant where AR was deployed to train new employees. Instead of relying solely on manuals, trainees used AR to interact with virtual simulations of equipment, accelerating their learning curve. Similarly, AR-assisted inspections have enabled engineers to detect anomalies that would have been missed during traditional checks. While adoption is still in its early stages, the potential for AR to enhance safety, efficiency, and collaboration in chemical operations is undeniable. As one industry expert observed, "AR bridges the gap between the physical and digital worlds, making complex processes accessible and intuitive." Why use Digital Twins?Digital twins have emerged as a cornerstone of innovation in the chemical sector, offering a virtual replica of physical assets that enables real-time monitoring, predictive maintenance, and process optimization. By simulating operations in a digital environment, companies can identify inefficiencies, test new workflows, and anticipate equipment failures before they occur. One prominent use case comes from a global chemical company that leveraged digital twins to optimize its energy consumption. By modeling different production scenarios, the company achieved a 15% reduction in energy use while maintaining output levels. Similarly, digital twins are being used to enhance safety by running virtual hazard simulations, ensuring that potential risks are addressed without interrupting operations. The potential for digital twins to revolutionize the industry is vast, offering a safer, more efficient, and sustainable future for chemical production. |
A race to innovate
What has evolved most strikingly since 2018 is the urgency. The "wait-and-see" approach has largely been replaced by a race to innovate, spurred by regulatory pressures and the looming specter of climate change. Companies that once hesitated to invest in digital tools are now piloting ambitious projects like predictive maintenance powered by AI or real-time monitoring of carbon footprints. Success stories abound, but they often highlight the challenges as much as the triumphs. For instance, a major player in Flanders invested heavily in a digital twin of its production facilities, only to discover that legacy equipment needed extensive upgrades before the technology could deliver on its promise.
In both reports, the message is clear: digitalization is not a one-size-fits-all journey. Each company’s path is shaped by its size, resources, and position within the value chain. What remains constant, however, is the need for collaboration—between industries, governments, and research institutions—to overcome shared obstacles and unlock the full potential of digital technologies.
Catalisti continues to guide the industry through this transformation and can help companies develop innovation projects with partners.